|
ACCESS THE FULL ARTICLE
No SPIE Account? Create one
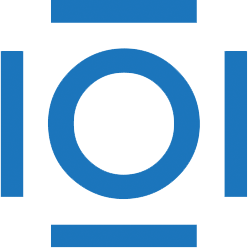
CITATIONS
Cited by 12 scholarly publications.
Wafer bonding
Semiconducting wafers
Plasma
Annealing
Microelectromechanical systems
Silicon
Metals